Computer Vision Station Prototype for Biscuit Tiles Quality Control
The visual inspection In ceramic tile industry in Croatia is carried out manually using specially trained and skilled workers. Currently in industry biscuit and crude tiles are not visually inspected for defects. Fatigue, illness and other subjective factors significantly influence workers percentage of found defects and classification quality. This project proposes a prototype computer vision station (CVS) for real-time biscuit tile defects detection. Proposed CVS should be mounted on a production conveyor line before the kiln. The CVS should reduce damaged or defected product percentage in crude and biscuit stage. Therefore, CVS should reduce cost due to energy saving and savings in raw material because the defected tiles are detected and eliminated before the firing process. In addition, shortened time of detection could increase production capacity.
In this TTP, we are designing computer vision station prototype based on mechanical construction or housing and computer vision system with camera, lighting, and industrial computer. Prototype system is developed for production line in ceramic tiles factory for detection of edge defects, corner defects and surface defects (spots, cracks, texture anomalies, etc.). The real time application of computer vision is growing in complexity because:
- ceramic tiles dimensions are in range from 20x20 cm to 45x50 cm, larger image resolutions are necessary and the picture size is growing also;
- the production line speed is increasing because of larger production capacity, production speed more than 60 tiles/s, or so the tiles are running in less than one second;
- hard deadline for real time application, all image processing algorithms must finish before the next tile.
Because of these specification limits CVS should be implemented in high performance parallel hardware architectures.
The partner company is Keramika Modus d.o.o., ceramic tile factory from Orahovica, Croatia. The total production in Keramika Modus d.o.o. was around 2 million m2 and total income was more than 10 million €. If the biscuit and crude tile defects are just 1% that is equivalent to income of more than 100.000 € estimated by the factory (cost of glazing and burning) for all production lines. Actual total percentage of defected crude/biscuit tiles are several percentages. Successful detection of faulty biscuit and crude tiles would save on the cost of glazing and gas in the firing process.
The CVS consists of metal housing, shown in the figure above, mounted on the conveyor line. Metal housing has several fans mounted on the top for air filtering and dust removal. LED light system, area-scan camera, parallel processing unit, digital I/O interface and tile proximity sensor are built in inside the housing. LED light system is controlled by a custom made control board with the developed application. Proximity light sensor marks the start of the tile image acquisition. Area-scan camera acquires the tile image and sends it via USB 3.0 interface to the parallel processing unit. Parallel processing unit executes all image processing algorithms and informs the user using built in LCD monitor and buzzer. The unit is based on core i7 CPU and Nvidia GTX 960 GPU.
The user-friendly MFC (Microsoft Foundation Class) based GUI application is created (main windows of the application are shown in the figure above). The developed application communicates with the LED control system, area-scan camera and digital I/O interface. All developed algorithms are implemented in C++ language using OpenCV and Nvidia CUDA libraries. Image processing is executed in several stages: image acquisition and distortion correction, image thresholding, edge defects detection, corner defects detection, surface defects detection and results displays. Tiles are classified as correct (no defects) or defected (have edge, corner or surface defects). The algorithms are implemented using sequential execution and parallel execution with windows threads and Nvidia CUDA.
Preliminary results show the maximum execution time below 900 ms that satisfies defined real-time requirements. The defect detection results, shown in the figure above, are promising. In the depicted graph less than 2% of biscuit tiles with defects are classified as non-defected, less than 0.5% tiles with no defects are classified as defected, while more than 98% are correctly classified. Possible savings in costs are at minimum 40.000 € per one production line, as estimated by the company.
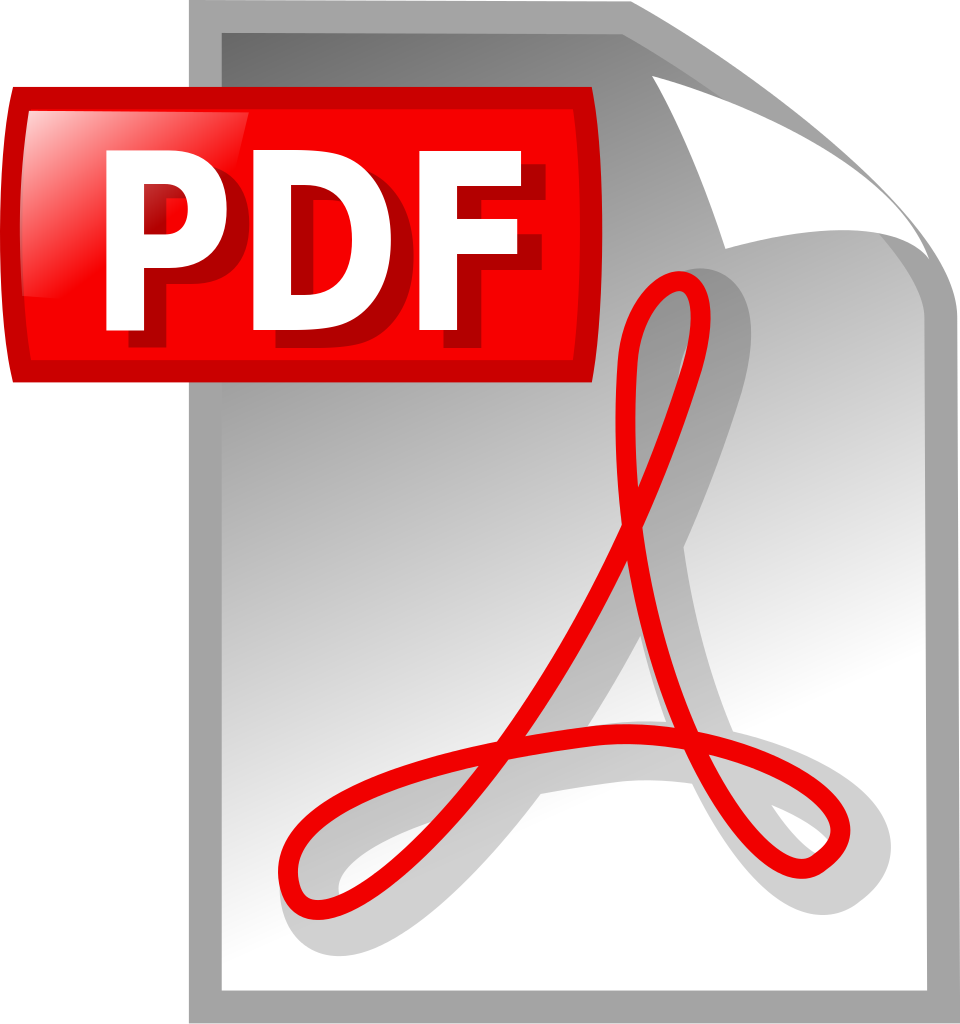
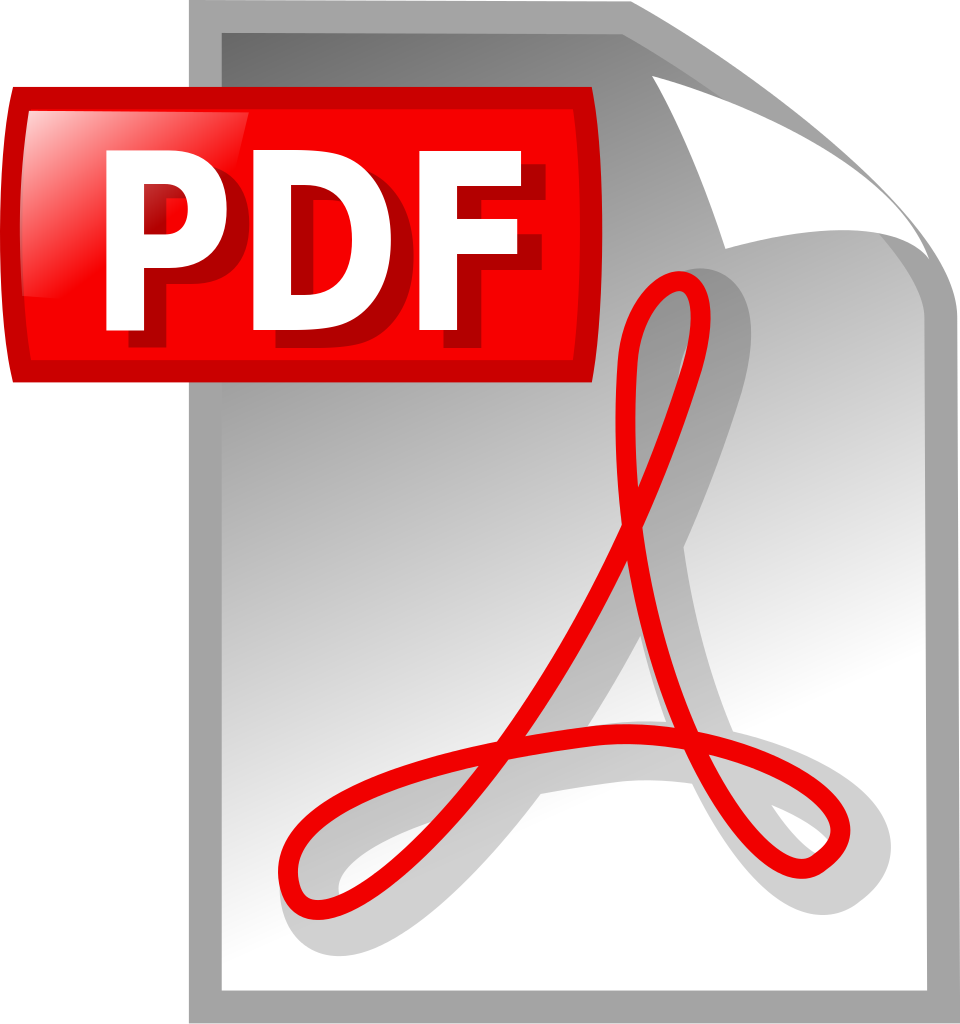