Fast Connected Component Analysis (CCA) for flexible high-speed image processing
The Connected Components Analysis (CCA) block (IP), which is transferred, enables with its design-time and run-time flexibility a fast deployment of various X-ray scanner based food inspection systems. This block is vital for many new Wipotec products that will use the new high-speed X-ray scanner (faster than 120m/min). The CCA engine is the last stage of an image processing chain where the final decision of the overall processing is made. It is a complex and highly sophisticated IP-block that might cause a bottleneck if not designed carefully. This block is accelerated to achieve highest possible throughput at high energy efficiency to keep the heat. It is integrated in Wipotec’s food inspection image processing chain in order to enable faster than 50ms scan times per inspection. An example of a food inspection and detection (clipped sausages) is shown in Figure 1 below.
Current installations of the company Wipotec GmbH are using standard general computing systems, such as the Intel i7-Core platform. These systems offer a large flexibility to support different food product inspection systems (box, bottle, fluid, pizza, wheat, etc.), however, their processing throughput reached its limit. Thus, a more tailored hardware and software is required to achieve higher scanning speeds. This hardware is a specialized FPGA solution including a new PCB (printed circuit board) and a new embedded software solution, which allows a flexible programming of the FPGA.
Figure 2 - CCA Processing: The connected components of the input image (A) are labeled (B). The connection table is then extracted forming a label connection and data table (C). The labels and data are unified (D) from the connection graph (E). Queries, such as “maximum intensity connected components” or “area of a connected component”, can be gathered from the unified table. Figure (F) shows the CCA as a hardware accelerator to the ARM core inside a ZYNQ FPGA subsystem.
The CCA processing and the CCA block implementation, as shown in the Figure 2, is seamlessly integrated into Wipotec’s new system and provides the necessary performance. Wipotec supported the University by providing the needed test hardware and food inspection know-how. Various test cases were enrolled to enforce employment and thoroughly testing of the CCA block to verify its correctness and flexibility. Two demonstrators in form of prototypes are currently in development to assess finally the CCA’s performance and functionality inside the processing chains. Thus, a high quality CCA block IP can be released to Wipotec after the final regression test phase and validation. The CCA block will be then part of a high available industrial processing chain in order to detect particles, impurities, metal, etc. in food products. Due to many computational scenarios that were covered at design time, the block is able to provide high runtime flexibility. Moreover, the CCA block is designed in such a way that it allows further extension in the future. As a result, new high-speed food scanners based on this new advanced image processing chain for upcoming market segments can be developed.
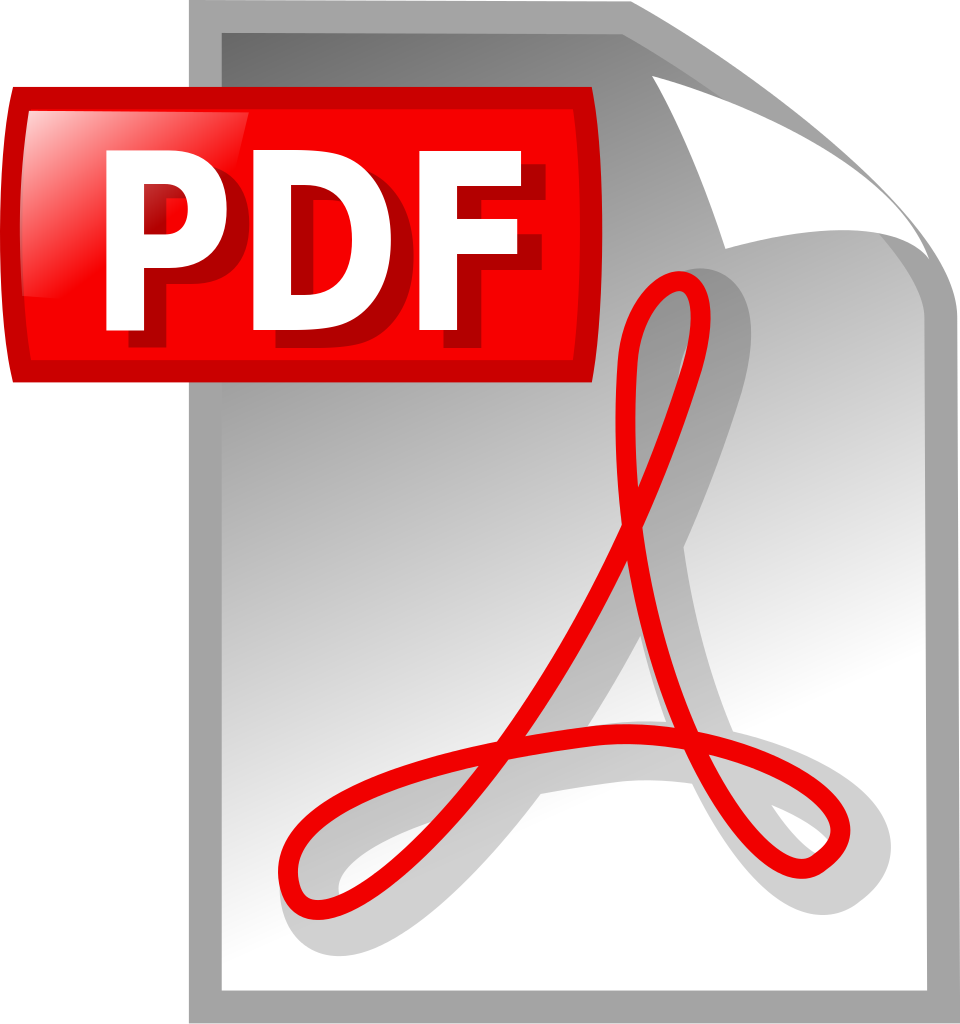